Pharma Utilities
Pharma
Utilities
Pharma Utilities are backbone for the Pharmaceutical Industry, Good Process & Utility Piping is fundamental to the success of any pharmaceutical or biopharmaceutical facility. In pharmaceuticals, critical utilities like WFI, RO/DI, Compressed Air, Nitrogen, Air Handling Units (AHU) and HVAC (Heating, Ventilation and Air Conditioning) systems support the manufacturing process.
Bio Clean with In-house Design team and installation team helps the Client to select the right utilities design and product makes.
Water System
We Provide Complete Solutions for Generation and distribution of water system for pharmaceuticals facility to set up with the objective of facilitating human health with medicinal products in accordance with the latest pharmacopeia. This includes right from Pre-Treatment, Double pass Reverse Osmosis systems, Electro De ionization systems and water for injection Multi column Distillation plants and pure steam generators (PSG).
One of the general principles which apply to any type of purified water systems in pharmaceuticals entails prevention of any microbial and physical recontamination.
One of the general principles which apply to any type of purified water systems in pharmaceuticals entails prevention of any microbial and physical recontamination.
There are three often used different types of industrial water filtration systems in pharmaceuticals :
- Ion exchange is one of the most desirable types of purified water treatments. It involves separation of watersoluble undesirable ions and exchanging those ions with desirable ones. Therefore, this water treatment technology focuses on altering the ionic composition in a desirable direction. Due to its ease of operation, minimal maintenance, the ion exchange method is mostly preferred in pharmacies as a type of purified water system.
- Reverse osmosis (RO) entails applying pressure to the concentrated solution in an osmosis process, thereby disrupting the natural osmotic flow. As a result, water starts flowing from the more concentrated to the less concentrated solution. It is strongly advised that RO systems being utilized for pharmaceutical manufacturing be designed for control of bacteria. RO units are often susceptible to microbial fouling and must be cleaned thoroughly and regularly.
- Distillation is another widely used type of purified water system in pharmaceutical practice is distillation. As a general principle, the first ten to twenty percent distillate must be discarded because the feed water contains innumerable volatile substances. The same case applies to the last twenty percent to prevent excessive dryness which would result in solid impurities contaminating the previous distillate. Heat is used to boil the liquid mixture containing volatile components. Later on, condensation is used to recover the vapor
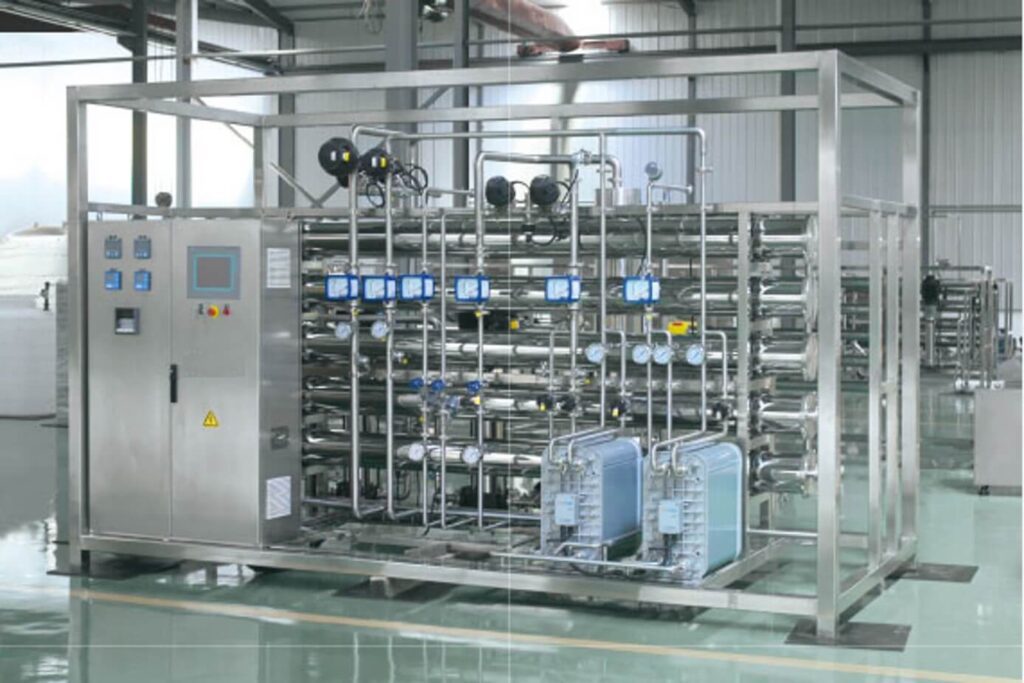
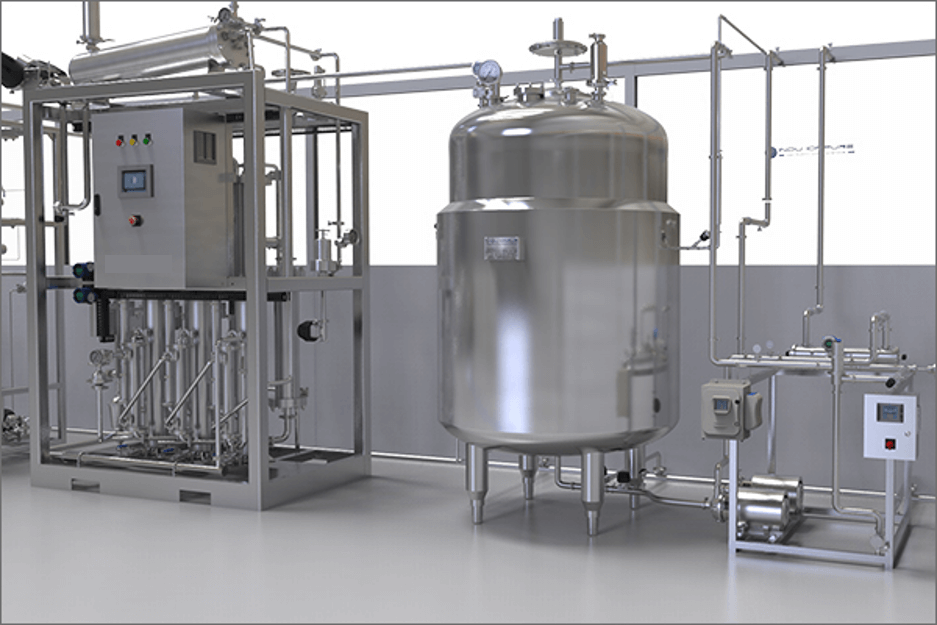
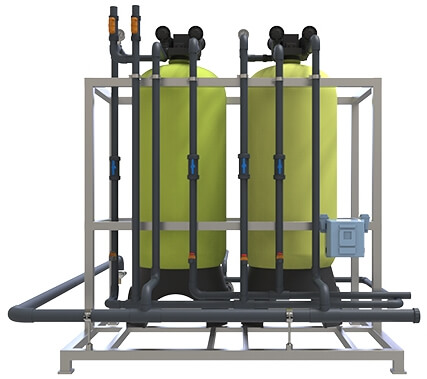
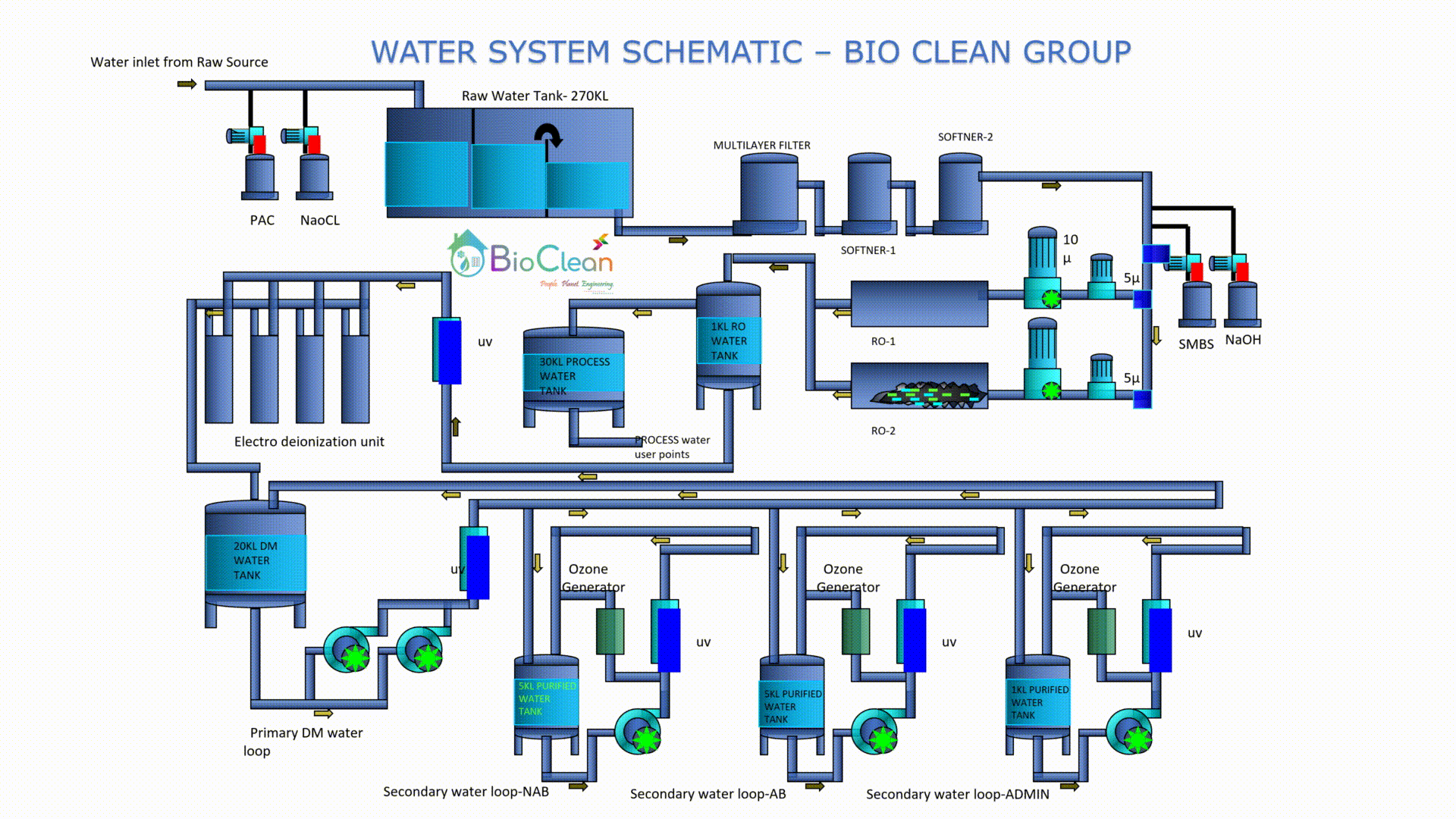
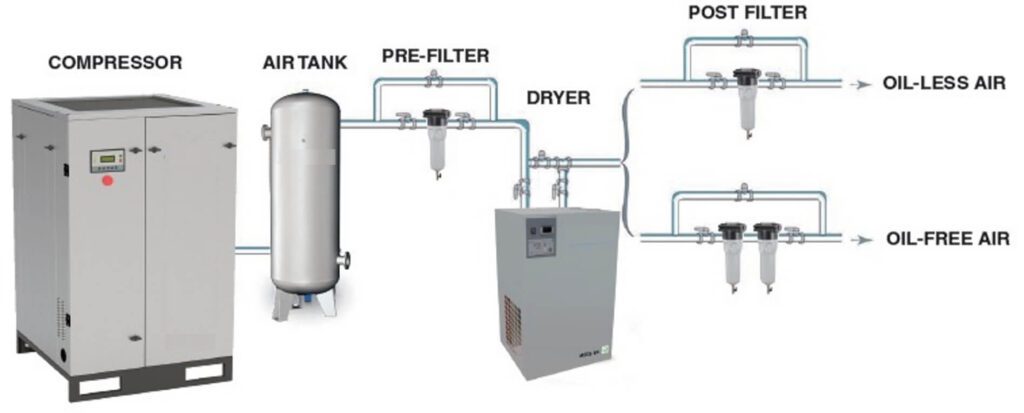
Compressed Air
Air Compressor is one of the most essential utility machines for the pharmaceutical industry. Ensuring the engineering parameters of the industrial compressor as well as maintaining the hygiene standard of the air at the same time is a complex task. This often creates a decision-making challenge while selecting an air compressor for a pharmaceutical factory. Therefore, this study discusses the most important selection criteria of an air compressor to be used in the pharmaceutical industry. Among all the criteria, 7 measurable criteria have been sorted out to be utilized in a Multi-Criteria Decision Making (MCDM) technique, the Technique for Order Performance by Similarity to Ideal Solution (TOPSIS) method. In this study, electricity consumption, free air delivery, maximum working pressure, noise level, installation surface area, oil content in the air, and solid particulate filter have been taken as criteria in the case study of selecting the best compressor. Among the 5 alternatives, compressor A4 has obtained the most performance score by the TOPSIS method, thereby finally selected in this study. The discussion about the selection criteria of air compressors for pharmaceuticals and the selection framework presented by utilizing the TOPSIS method is expected to help the industrial managers of pharmaceuticals to overcome their decision-making challenges of compressor selection.
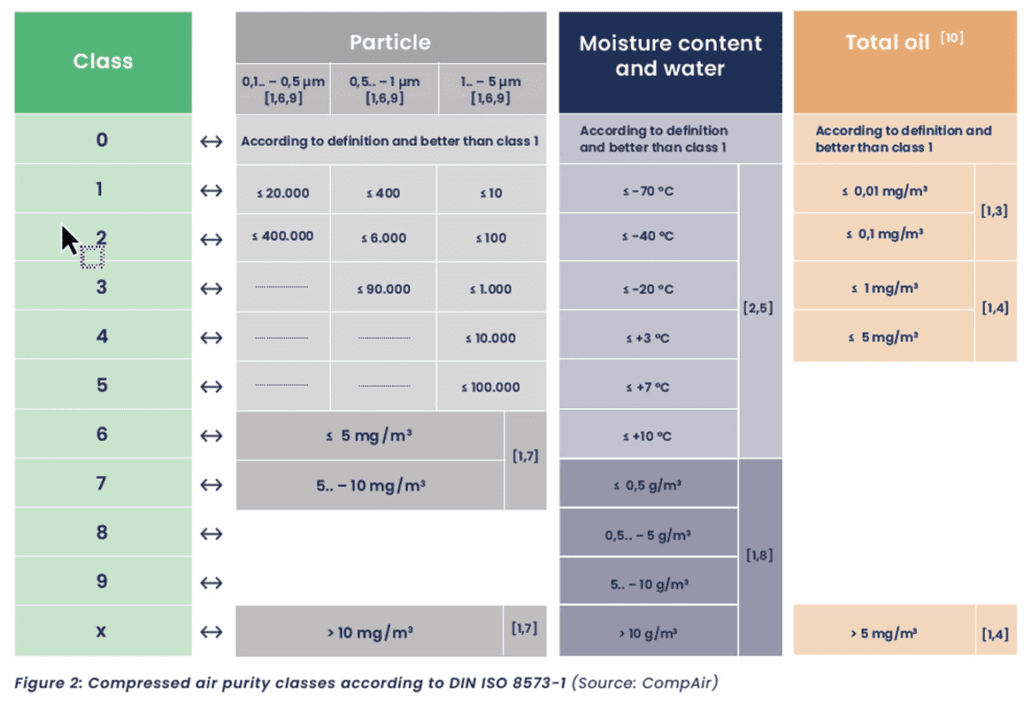
Steam Generation
Clean Steam is used in the Pharmaceutical and Healthcare Industries in processes where the steam or its condensate can come into contact with a pharmaceutical or medical product and cause contamination. In such cases, steam from a conventional boiler (often called utility or plant steam) is unsuitable because it may contain boiler additives, rust or other undesirable materials.
The use of clean steam is determined by the rules of Good Manufacturing Practice (GMP). These are general rules applicable to pharmaceutical manufacture, detailed in the Code of Federal Regulations (CFR Title 21, Part 211). They do not provide any specific recommendations regarding steam, but do present the general requirements of facilities, systems, equipment and operation needed to prevent contamination of pharmaceutical products during their manufacture
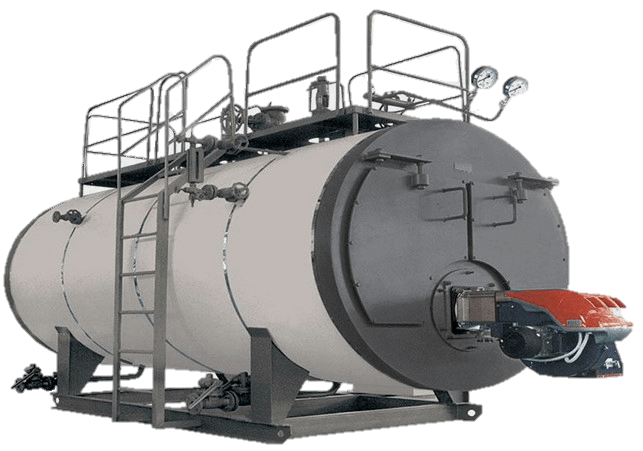

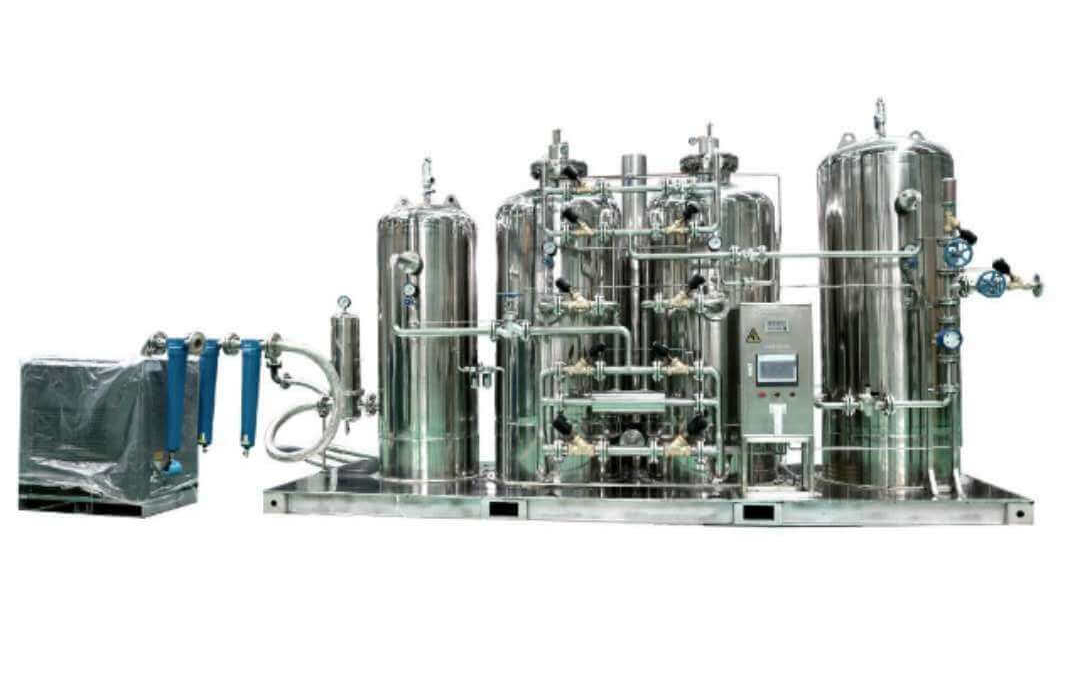
Nitrogen Generation
Nitrogen gas is required for a number of critical processes in the pharmaceutical industry including blanketing, inerting, and sparging pharmaceutical materials during the manufacturing, pre-packaging, packaging, and distribution processes. Purity level requirements will vary depending on the application or materials that the nitrogen gas is being used for at any given time. Generally, however, the pharmaceutical industry demands nitrogen gas purity levels that can range between 99% and 99.999%. Higher purity levels are typically required for more oxygen sensitive materials.
Related Services
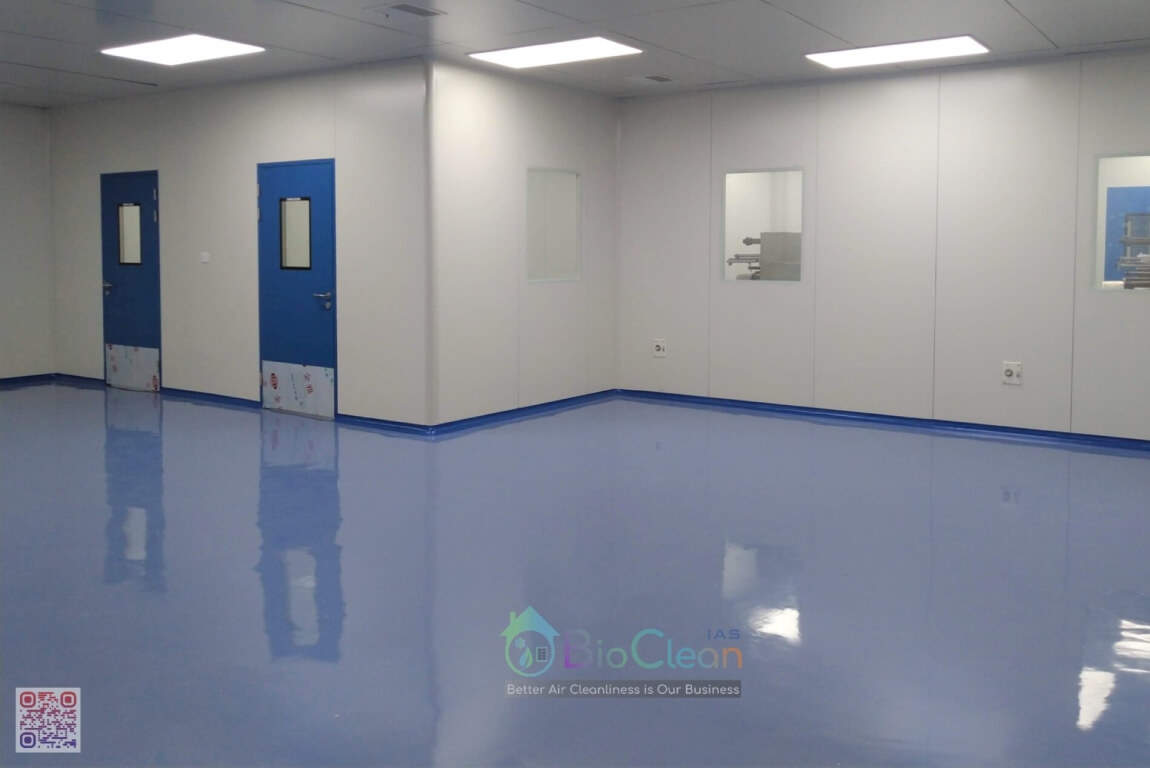
TURNKEY CLEANROOM SOLUTIONS
WALKABLE CEILING PANELS
FIRE RATED DOORS
METAL DOORS
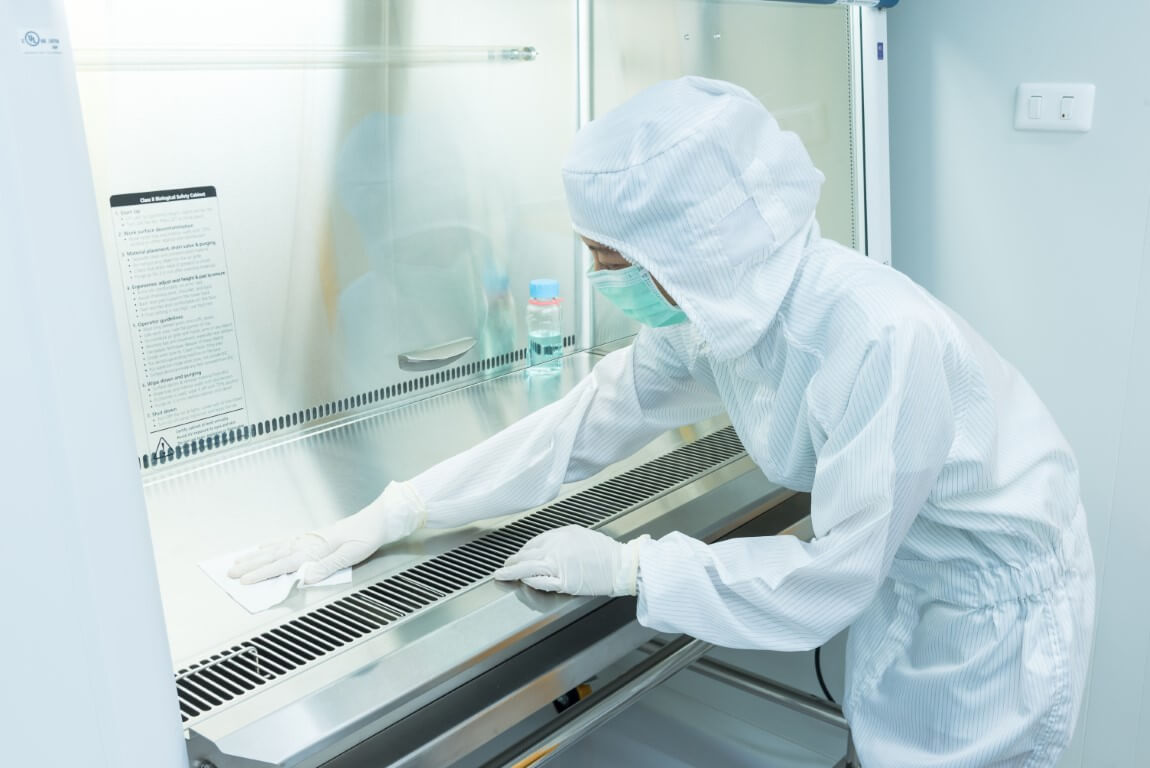
CLEANROOM EQUIPMENT
STATIC AND DYNAMIC PASSBOX
BIO SAFETY CABINETS
HEPA / ULPA FILTERS

ENGINEERING CONSULTANCY
FROM IDEA TO CONCEPTUALIZATION
PROJECT MGMT. AND CONTROL
INST, COMM & VALIDATIONs
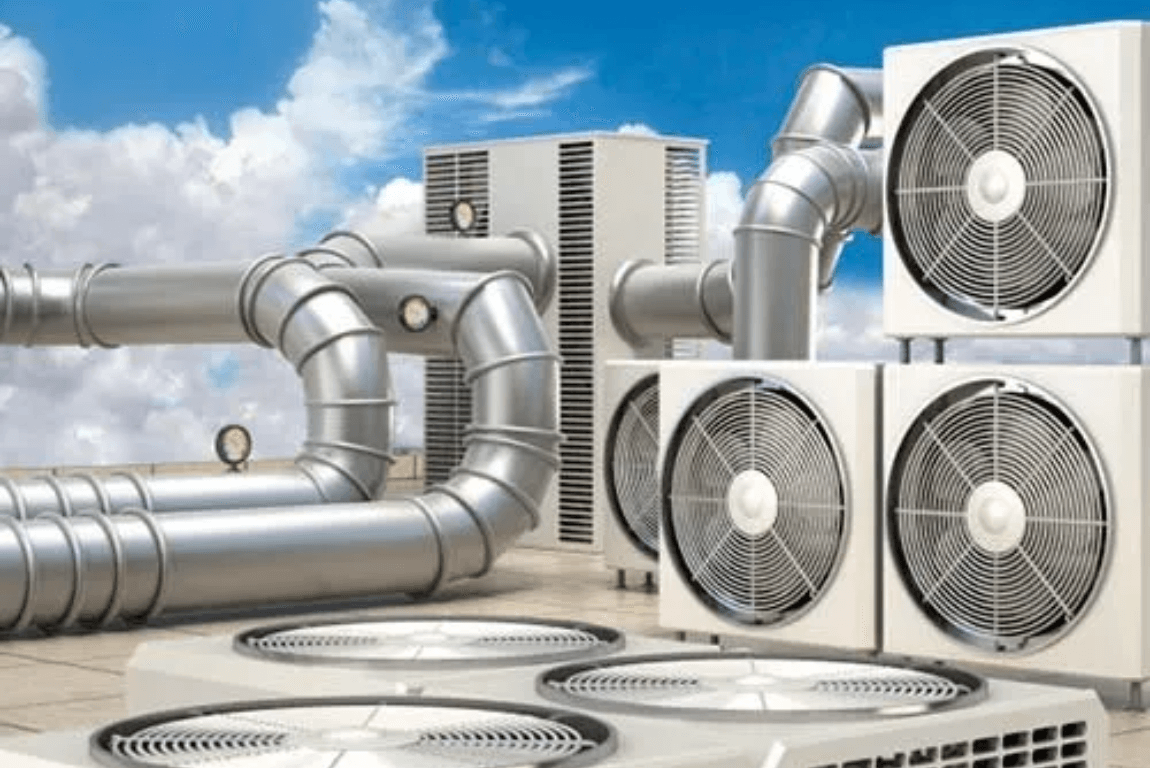
TURNKEY HVAC SOLUTIONS
PRE FABRICATED DUCTS
AIR HANDLING UNITS
DEHUMIDIFIERS

PHARMA PROCESS EQUIPMENT
TRACK AND TRACE SYSTEM
PACKING EQUIPMENT

FIRE FIGHTING SYSTEM
GAS SUPPRESSION SYSTEM
FIRE ALARM SYSTEM
FIRE EXTINGUISHER